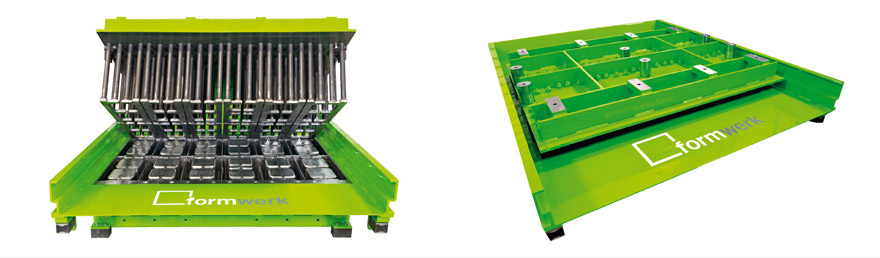
formwerk hollow block mould – Zenith 913
This novel design concept was developed in consideration of many years of valuable customer experiences. The economic production process and the high product quality are the focus.
The function
An important point of development is the vibration-friendly mould insert boxes. The light mould bottom is optimally designed to achieve a good and fast compression.
With just two high-frequency vibrators, excellent compression results are achieved. For a faster compression, it is possible to install up to four high-frequency vibrators. The end walls and mortar grooves are designed from 4-5 mm thick walls. Combined with specially used high-strength premium alloy steels, this leads to particularly effective vibration characteristics. The results are equally beautiful stones from an efficient production process. The precise manufacturing of core assemblies as modular components is a guarantee for economic production processes. The ability to reorder original formwerk core assemblies as spare parts ensures a smooth production process without costly downtimes. The tamper head of the mould is based on a balanced and solid construction with considerable rigidity of the assembly.
When lowering, a high kinetic energy is built up, which leads to a pressing effect - a guarantee for good and fast compression. The stripper shoes at the tamper head of the mould are installed as individual components using bolted pins on the tamper plate. If necessary, the stripper shoes can be easily and quickly removed. Bolted pins with stripper shoes can be quickly redelivered as spare parts at any time. The precise mould design guarantees optimal interaction between the tamper head and the mould bottom.
The service
Contact us for comprehensive advice and individual planning.info@formwerk.org